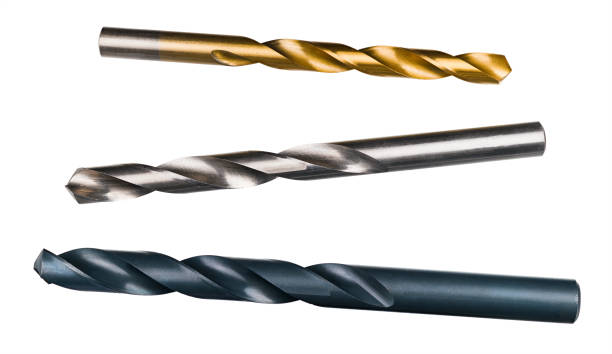
Selecting the appropriate drill bit coating is crucial for optimizing performance and extending tool life. This guide explores common coatings—black oxide, titanium nitride, and diamond powder—and their benefits.
Black Oxide Coating
Black oxide is a chemical treatment applied to high-speed steel (HSS) drill bits, resulting in a distinctive black finish.
Benefits:
- Corrosion Resistance: The coating provides a protective layer that resists rust, enhancing durability.
- Reduced Friction: It decreases friction between the bit and work material, leading to smoother drilling and less heat generation.
- Cost-Effectiveness: Black oxide-coated bits are economical and suitable for general-purpose drilling.
Ideal Applications:
Black oxide bits are versatile, performing well in drilling wood, plastics, and soft metals like aluminum. They are not recommended for hard metals or abrasive materials.
Titanium Nitride (TiN) Coating
Titanium nitride (TiN) is a hard ceramic material applied as a thin coating to metal surfaces, recognizable by its gold color.
Benefits:
- Increased Hardness: TiN significantly enhances the surface hardness of drill bits, extending their lifespan.
- Heat Resistance: It allows drill bits to operate at higher speeds without losing temper, maintaining cutting efficiency.
- Lubricity: The coating reduces friction, resulting in cleaner cuts and reduced wear.
Ideal Applications:
TiN-coated drill bits are suitable for drilling through metals, including steel and iron, as well as wood and plastics. They are not ideal for drilling hard metals like stainless steel or cast iron.
Diamond Powder Coating
Diamond powder coating involves embedding fine diamond particles onto the drill bit’s surface, creating an extremely hard and abrasive-resistant tool.
Benefits:
- Superior Hardness: Diamond is the hardest known material, providing exceptional cutting ability.
- Wear Resistance: The coating offers unparalleled durability, maintaining sharpness over extended use.
- Precision: Ideal for applications requiring fine, accurate drilling.
Ideal Applications:
Diamond-coated drill bits are perfect for drilling extremely hard and abrasive materials such as glass, ceramics, and composites. They are not suitable for drilling ferrous metals due to potential chemical reactions at high temperatures.
Choosing the Right Coating
Consider the following when selecting a drill bit coating:
- Material Hardness: Match the coating to the hardness of the material being drilled.
- Drilling Speed: Higher speeds may require coatings with better heat resistance.
- Budget: Balance cost with performance needs; higher-end coatings offer greater durability but at increased expense.
Understanding the benefits and applications of different drill bit coatings enables you to select the most suitable tool for your specific needs, enhancing efficiency and prolonging tool life.
You can also visit our partner site at www.drillbitsusa.com for more information.